The Process of Making Porcelain
1. Raw Material Preparation
Porcelain, being durable and lovely, starts with serious preparation of raw materials. The major components are kaolin, feldspar, and quartz, which are carefully chosen for their quality and purity. Kaolin, a clay material, provides plasticity and constitutes the body of the porcelain. Feldspar is a secondary flux, lowering the melting point of the mixture and facilitating vitrification during firing. Quartz adds hardness and strength to the final product.
The process starts by extracting the raw materials, which are later sent to the plant. The materials undergo a strong refining process at the plant. The raw material is crushed and ground into powder initially. The powder is blended with water to make a slurry. The slurry is filtered to eliminate the impurities and obtain an even-sized particle.

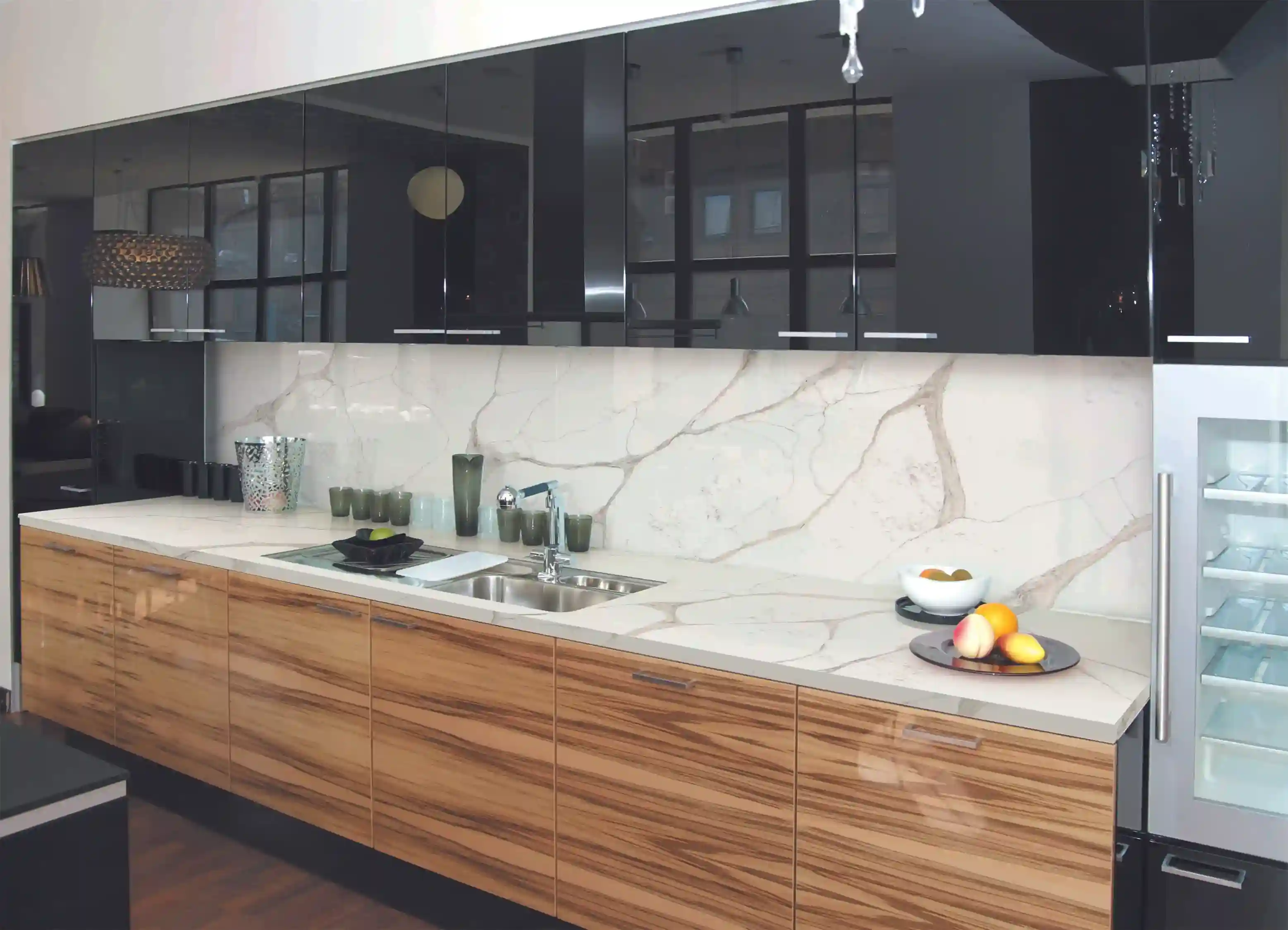
2. Forming
Porcelain forming is a painstaking process that develops raw materials into handsome, long-lasting products. It all starts with selecting quality clay, mostly kaolin, with feldspar and quartz. These are blended with water to produce workable, pliable material called porcelain slip.
The process of forming consists of developing such slips into desired shapes through several techniques. One common technique is slip casting, in which the slip is cast into plaster molds. Plaster is porous, and water gets absorbed by it, leaving behind a solid clay layer against the walls of the mold. Such a technique is best for producing fine details and complex shapes.
3. Drying
Porcelain drying is an essential phase in the production of porcelain items, making sure that the products achieve the required strength and stability prior to firing. This entails the careful evaporation of water from the porcelain body to avoid cracking, warping, or other flaws upon subsequent kiln firing.
To start with, when molded, porcelain holds a lot of moisture and hence is soft but brittle. Slow, controlled drying lowers the moisture content. This can be carried out naturally by drying air or by more sophisticated means, such as using drying rooms or chambers where temperature and humidity are controlled. Within these facilities, airflow, temperature, and humidity are carefully controlled to dry evenly, which is essential in protecting the porcelain items and their shape.
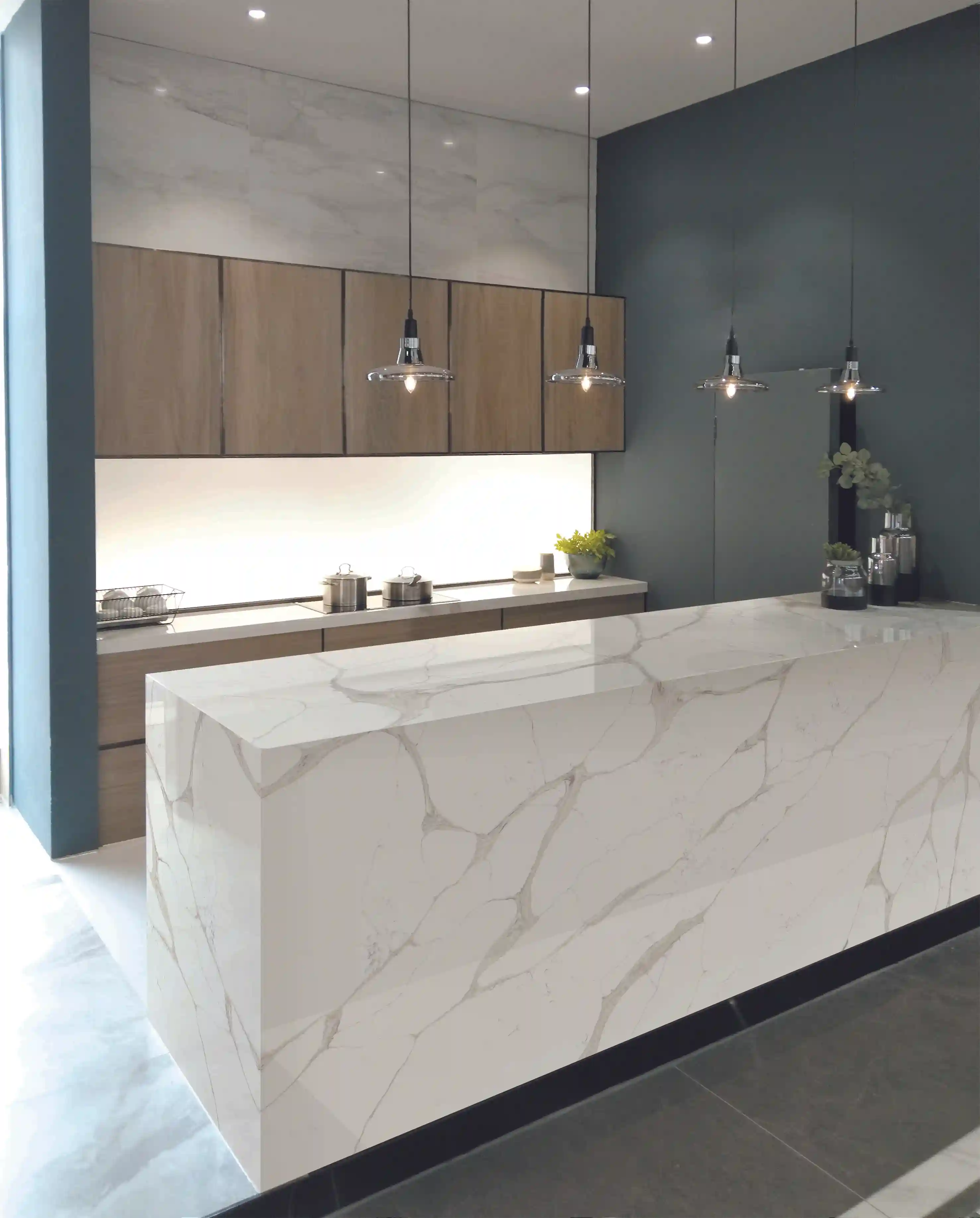
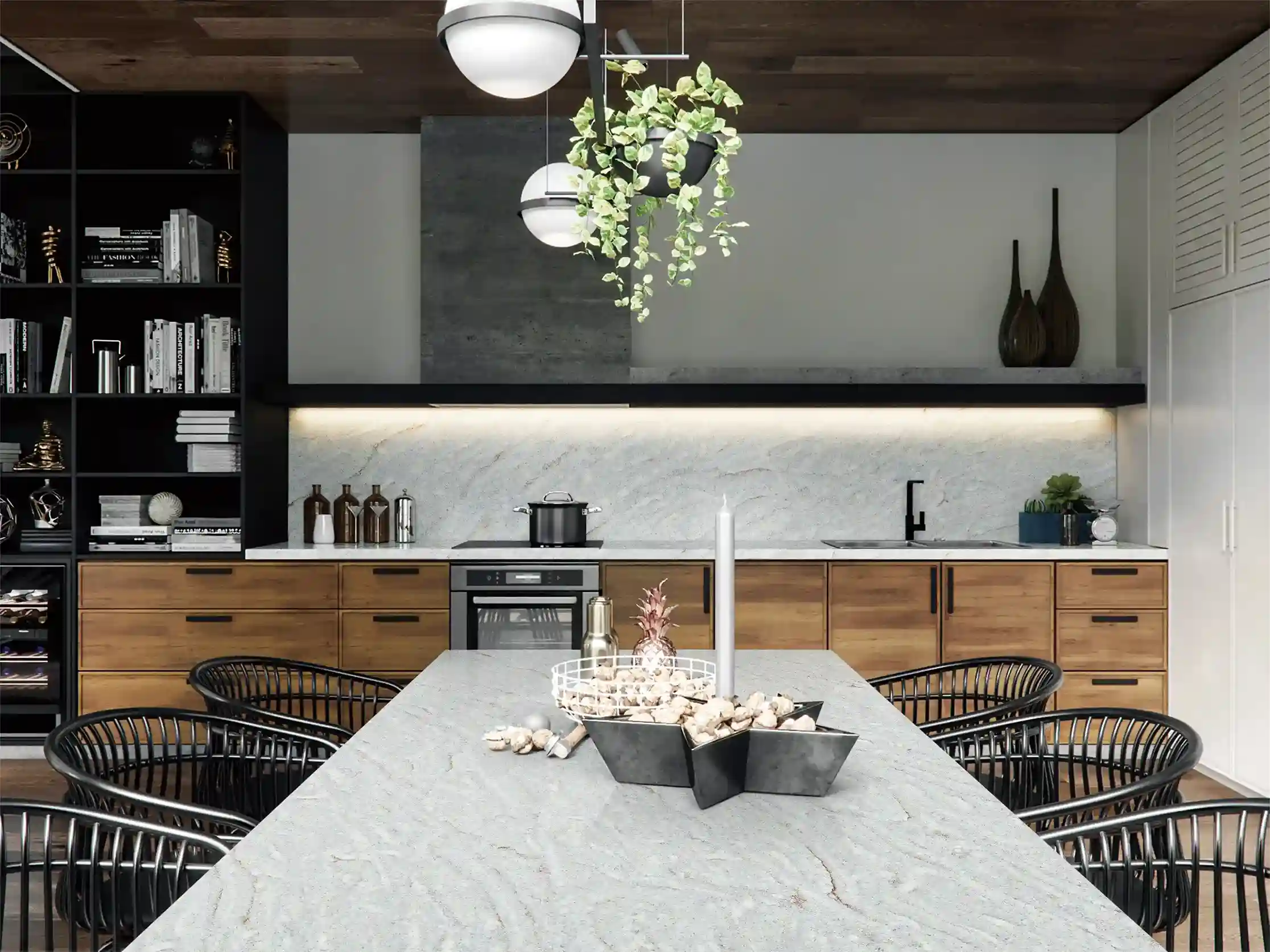
4. Firing
PFiring porcelain is a crucial production method for transforming raw materials into durable, glassy ceramic finished goods. Firing involves heating shaped porcelain in a kiln at extremely high temperatures, ranging from 1,200 to 1,400 degrees Celsius (2,192 to 2,552 degrees Fahrenheit). Elevated temperatures promote vitrification, a process where clay particles fuse and melt, resulting in dense, transparent, and non-porous finished products.
The process begins with bisque firing, the initial phase where the shaped clay is heated at a lower temperature to remove moisture and organic materials. This procedure strengthens the item to facilitate easier handling for glazing.
5. Glazing
Porcelain glazing is a process that enhances the physical appearance along with the functionality of porcelain tiles. It is the method of applying a liquid glass coating on the surface of the porcelain tile and then firing it with high temperatures. This serves to produce a shiny, hard, and water-resistant finish which enhances the physical appearance and longevity of the tile.
One of the most important advantages of glazing porcelain is that it is capable of creating a stunning, glossy finish that intensifies the color and pattern of the tile. Glaze is any color and can additionally include subtle patterns, making copying the look of natural stone, wood, or even fabric possible. With that level of versatility, application possibilities for homes and businesses are endless.

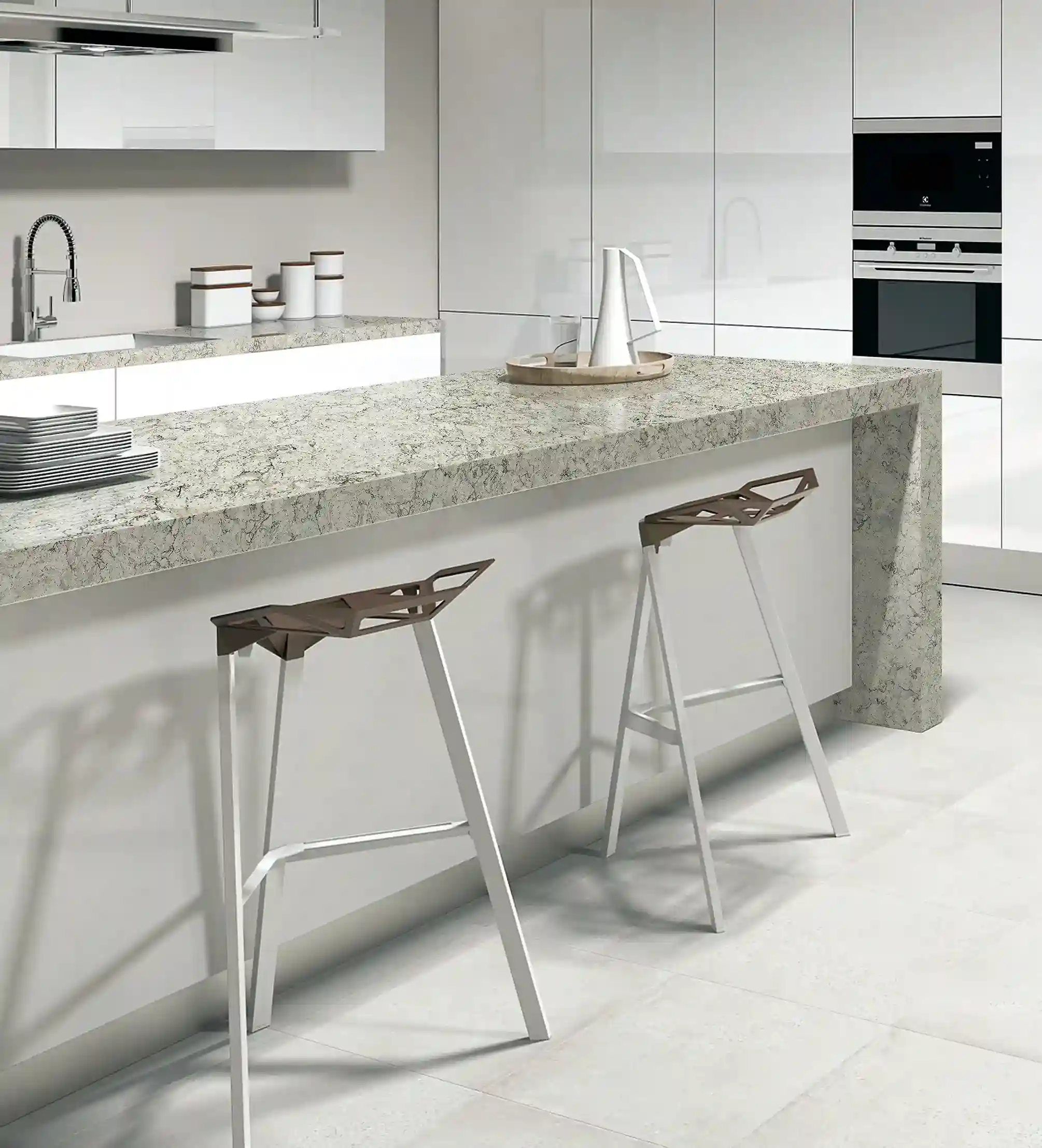
6. Quality Control
Quality controlled production The production of porcelain is a highly skilled, multistage and intense quality process in order to ensure durability, aesthetic and function over many years of use. It starts at raw material selection. Each product is made with only the purest materials available and is free of the impurities that could compromise the quality of the product.
When chosen, these materials are subjected to extensive laboratory testing and characterization. This step includes testing for chemical composition, particle size distribution and plasticity requirements which must comply with predetermined specifications.This operation is also the testing of the chemical composition, particle size distribution and plastic limitations that should be met according to the standards.